Gearing Up Bike Design: 3D Printing Transforms the Rider Firm's Innovation Process
- marketing1
- Aug 21, 2023
- 7 min read

Hunt Bike Wheels tests their rim profiles in the Friedrichshafen Wind tunnel in Southern Germany
As the world increasingly embraces cycling for commuting to work, exploring nature, working out, or racing, it is paramount for bike manufacturers to keep up with the ever-evolving trends and technological developments. The Rider Firm is the company behind one of the world’s leading direct consumer wheel brands, Hunt Bike Wheels, as well as other cutting-edge performance gear, components, and bike brands including Privateer Bikes, Cairn Cycles, and Dissent 133.
As they aim to produce high performance bikes and components that are within reach for not only the most affluent riders, their development process has to be smarter and more efficient than that of traditional bike brands with bigger budgets. Bringing 3D printing in-house, through the acquisition of a Form 3L large-format SLA 3D printer, was the company’s latest move to drive innovation and redefined their workflow.
While the main manufacturing hub for the cycling industry is Taiwan, the product development process for the Rider Firm happens at home in the UK, where the teams rely heavily on the Form 3L, mainly for prototyping. Dan Hicks, Development Engineer at Privateer Bikes and Patrick Brown, Design Engineer at Hunt Bike Wheels sat down with us to reveal some insights into their workflow and how the Form 3L helps the engineering teams to constantly innovate and bring out new products.
Hunt Bike Wheels: 3D Printing Full-Scale Functional Prototype Rims for Wind Tunnel Testing
The name Hunt Bike Wheels comes from the company’s mission to persistently hunt down all the little details that you can put into the product. The team of experienced engineers works tirelessly to create wheelsets that deliver exceptional performance on various terrains.
Through extensive research, development, and testing, they aim to enhance speed, stability, and efficiency by optimizing the aerodynamics of their wheels. In pro cycling, it’s all about marginal gains — the aerodynamic drag difference between wheelsets is minuscule, in the 2% to 5% range at 45 kilometers an hour, but this difference can mean just those few seconds that divide the first and the tenth place.
Patrick Brown walked us through the wheel development process; which starts with the engineers designing different rim profiles and testing them using computational fluid dynamics (CFD), which is essentially a virtualized wind tunnel. CFD analysis allows the team to identify the best-performing rim profiles which will later be tested in real life using 3D printed prototypes.
For their latest LIMITLESS wheelsets, the team tested approximately 45 different rim profiles through CFD analysis and identified the ones with the lowest drag and best crosswind handling characteristics. They ended up with four front wheels and three rear wheels that they proceeded to 3D print and test in the Friedrichshafen Windkanal in Southern Germany.
Thanks to the Form 3L’s large build volume, the engineers could print the bike wheels in five or six sections each, depending on the number of spoke holes used in the sections, and could fit four rim sections on the build platform at a time. After post-curing and post-processing, the printed parts were glued together with epoxy resin and built into functional prototypes, assembled with hubs, spokes, and tires.
Talking about the use of Grey Pro Resin, Patrick Brown says that the 3D printed wheels “are a bit soft, but they can take about 65% of the tension of a carbon fiber wheelset. So you build quite straight, quite true, good enough for the wind tunnel.”

Grey Pro Resin is a great material for prototyping as it can take about 65% of the tension of a carbon fiber wheelset.
In the past, Hunt Bike Wheels would turn to a third-party service provider to 3D print the different wheel sections, but this had many disadvantages. First, the engineers would have to send out the finalized wheel profiles two to three months out, which would slow down the process, and reduce the room for flexibility. In fact, now that they have the Form 3L, Brown admitted that, in their latest project, they “got the last prints off the printer right before [they] left”, meaning they could iterate until the very last minute. The outsourced parts also weren’t strong enough to pump the tire up to pressure and some of the parts would crack, rendering them inapt for testing.
"I can now simulate for much longer and keep developing new profiles."
Patrick Brown, Design Engineer at Hunt Bike Wheels
“We need to be able to pump the tires up to a pressure where the tire makes the right shape on the wheel. It's really important to us that the prints are not only accurate geometrically, but they're strong enough so we're getting the right aerodynamic profile over the whole thing.” These critical requirements during the development process were fulfilled by Grey Pro Resin which demonstrated great geometric accuracy and an impressive ability to take up to three and a half bars of pressure from the pumped-up tires. Brown also highlighted the great surface finish that Grey Pro Resin had to offer was a key element when testing for aerodynamics.
"[In the wind tunnel] they run on a roller - so the wheel is spinning at 45 kilometers an hour."
Patrick Brown, Design Engineer at Hunt Bike Wheels
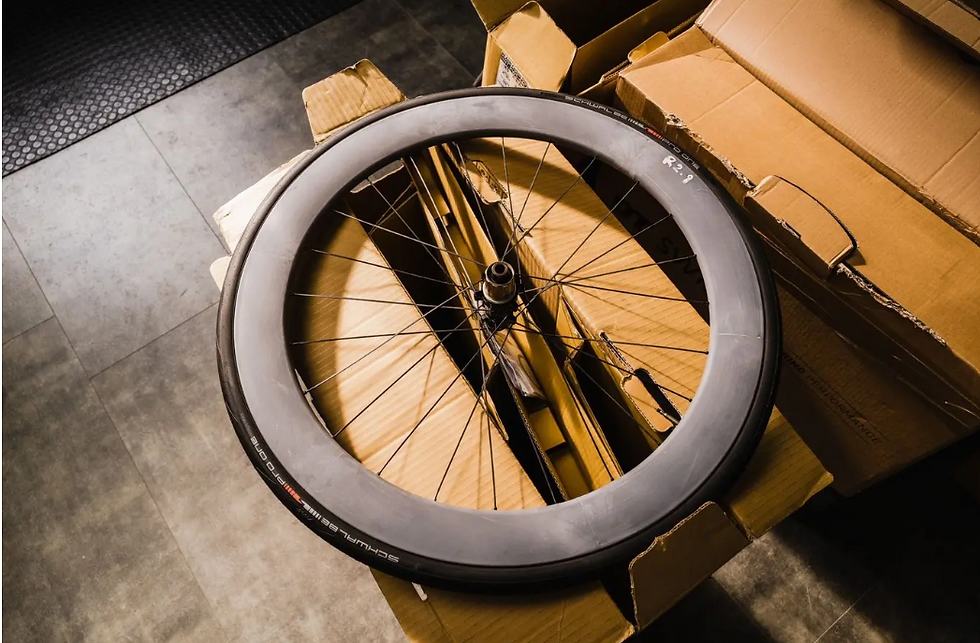
Grey Pro Resin’s great surface finish was key for aerodynamic testing.
In house 3D printing also empowers the engineering team to iterate more, even while cutting down on costs. In their outsourcing days, Hunt Bike Wheels would spend approximately £2000 on a single rim prototype. These costs have now been cut down by 90% to around £200 thanks to the Form 3L.
“It means when we go to the wind tunnel we can take a much larger number of wheels, so that we can validate broader CFD studies. It means we skip three or four cycles of product iteration to get to a premium product. Now every time we do a product, we know the first time we release it it’s in a very good place” says Hicks.
"I can now simulate for much longer and keep developing new profiles. Having this flexibility in-house has been a big benefit for us."
Patrick Brown, Design Engineer at Hunt Bike Wheels
The Form 3L now represents an essential part of the business model as it allows the Rider Firm to stay ahead of the competition. In fact, Hicks says that “by being clever about how we prototype, by being lean with our business operations, we are giving you a wheel that has the same aerodynamic performance as bigger companies at half the price.”
Privateer Bikes: Pushing Boundaries With Full Bike Frames and Rapid Prototyping
At Privateer Bikes, the engineering team uses the Form 3L for a range of prototyping applications, including prototyping whole bike frames as well as frame protectors.
Working on a new range of bikes, the engineering team at Privateer Bikes has printed entire bike frames and some of the more complex sections of the frame in different sizes. This allowed them to fit components on them, for example, pressing bearings and suspension forks into the frame, to ensure manufacturability and double-check the clearances for different frame sizes. “We can check clearances, how it assembles, if components fit, or if something's going to bang when the suspensions move.”
Additionally, printing the whole frame has allowed the in-house graphic designer to spray paint it to try out concepts with the artwork, and to come up with the decals for the new bikes. The frames were 3D printed in Grey Pro Resin in multiple smaller prints, which are later assembled and glued together. Once the bike is assembled and the parts are glued together, the bike can take quite some stress and “you can be reasonably rough with the handling of them.”
“It’s been very useful having the 3D print, just to be able to play with something,” says Hicks. He adds that “for the marketing teams, it’s good for them to have something tangible, because then when we’re talking about a esign, you can communicate it a lot better by just having the prop and showing people.”
Hicks points out that the Form 3L has been especially beneficial for prototyping custom frame protectors for their bikes. On a mountain bike, the chain often bumps into the chainstay which can get quite noisy and could damage the frame. That’s why the team has developed these tailored frame protectors made out of rubber that stick to the chainstay.
Normally, the team wouldn’t have the possibility to prototype these kinds of parts, so they’d just send the design to the Taiwanese supplier, who would make the production tooling and send them a sample of the final part. This whole process normally takes three to four months and costs around $3,000 or $4,000. This would have made it hard to tweak, iterate and optimize the part, since any design change would have required new tooling to be made, meaning that they’d have to pay again.

The Form 3L has been a great tool to print the frame protectors prototypes in Flexible 80A Resin.
With 3D printing, the engineers at Privateer Bikes can print three or four designs and prototype very quickly. “It costs us nothing to change the design, and that means when we send a production file over to the manufacturer, we can commit to production straight away,” says Hicks. He adds that this saved them probably about six months in the project, and about $4,000 or $5,000 in production tooling.
"When we send a production file over to the manufacturer, we can commit to production straight away."
Dan Hicks, Development Engineer at Privateer Bikes
The material of choice for this particular application was Flexible 80A Resin, which “is about the right durometer”, making it ideal for functional prototypes that are directly stuck on bikes for testing. They have been testing these protectors on the bikes for several months, checking where the chain still hits, where it still makes noises, and iterating based on those results.
"We can do a lot of the design for manufacture because it is a lot easier when you’re physically looking at it to think about split lines in tooling and kind of how that's going to work."
Dan Hicks, Development Engineer at Privateer Bikes
Rapid Response to Changing Trends With 3D Printing
"Everybody rides bikes differently, we don't know what people are going to be doing in two years' time. But we are now in a really good place to respond quickly to changing trends, to jump on new things."
Dan Hicks, Development Engineer at Privateer Bikes
In the near future, the Rider Firm is looking to develop more e-bikes and their components. These bikes involve more complex designs, as Hicks pointed out that “the more components you have to fit, the more difficult it is” and that 3D printing will allow them to prototype all those setups.
“Everybody rides bikes differently” so the team at the Rider Firm is curious to see what people will be doing. With the Form 3L in their arsenal, the company is now in a good position to respond to changing trends quickly as they continue to strive for innovation.
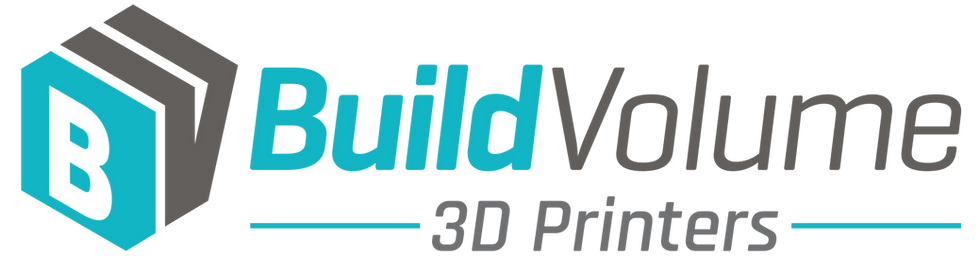
Click here provide members with discounts on over-the-counter medications, vitamins, and health essentials, promoting better health management and cost-effective wellness solutions. kaiserotcbenefits.com - more details here
Click here help you find recent death notices, providing information about funeral services, memorials, and tributes for loved ones in your area. obituariesnearme.com - more details here
Click here? Many users have had mixed experiences with the platform, so it's important to read reviews and verify deals before booking. istravelurolegit.com - more details here
AV在线看 AV在线看;
自拍流出 自拍流出;
国产视频 国产视频;
日本无码 日本无码;
动漫肉番 动漫肉番;
吃瓜专区 吃瓜专区;
SM调教 SM调教;
ASMR ASMR;
国产探花 国产探花;
强奸乱伦 强奸乱伦;
무료카지노 무료카지노;
무료카지노 무료카지노;
google 优化 seo技术+jingcheng-seo.com+秒收录;
Fortune Tiger Fortune Tiger;
Fortune Tiger Fortune Tiger;
Fortune Tiger Slots Fortune…
站群/ 站群
gamesimes gamesimes;
03topgame 03topgame
EPS Machine EPS Cutting…
EPS Machine EPS and…
EPP Machine EPP Shape…
Fortune Tiger Fortune Tiger;
EPS Machine EPS and…
betwin betwin;
777 777;
slots slots;
Fortune Tiger Fortune Tiger;
google 优化 seo技术+jingcheng-seo.com+秒收录;
谷歌seo优化 谷歌SEO优化+外链发布+权重提升;
Fortune Tiger Fortune Tiger;
Fortune Tiger Fortune Tiger;
Fortune Tiger Fortune Tiger;
Fortune Tiger Slots Fortune…
gamesimes gamesimes;
站群/ 站群
03topgame 03topgame
betwin betwin;
777 777;
slots slots;
Fortune Tiger Fortune Tiger;
谷歌seo推广 游戏出海seo,引流,快排,蜘蛛池租售;
Fortune Tiger…
Fortune Tiger…
Fortune Tiger…
Fortune Tiger…
Fortune Tiger…
gamesimes gamesimes;
站群/ 站群
03topgame 03topgame