BuildVolume 3D designed and printed the flowers for the Miss South Africa 2018 Pageant on our Sinterit SLS pr
For fashion designers, all of the beauty contests are important, especially when it comes to the Miss Pageants. The apparel may help or squander the chances to win the competition. It is the story of how SLS 3D printing technology helped Ciska Barnard, the Bambshell® Swimwear designer create the unique collection for the Miss South Africa finalists.
Bambshell® is an exclusive swimwear label created by Melinda Bam, former Miss South Africa from 2011.
– The contestants showed off the Afrocentric Beauty collection which showcases the colorful complexities of African culture in a celebration of color and bold prints. Each print is custom designed for this range and incorporates a mix of ethnic, tribal and modern prints on voluminous capes, juxtaposed against the sleek silhouettes of the swimsuits – says Melinda Bam.
How it started
Fashion was always flirting with the technology, thanks to which it could develop and spread over the world. As people started to sew approximately 20 000 years ago, until the 19th century, it was time-consuming, hand-made process. That is why ladies in the 18th century had only a few clothes in their wardrobes. Not more than two dresses. The invention of the sewing machines completely changed the perspective and reduced the time consumption. But the fabrics weren’t changing for more than 150 years. Just after the WWII, international trade conflict which involved the US and Asia countries brought the specter of stopping supplies of the basic fabrics. That lead to synthetic materials innovation, so prevalent in a disco era in the eighties. But now we are watching the return to nature, to sustainable materials. Designers are devoted to the best fabrics and are sometimes stopped by its properties. Some shapes can’t be done from the natural textures. 3D printing seems to be the best solution.
From a costume to ready-to-wear fashion
While thinking about 3D printing in fashion, we still remember a lot of outer worlds looking, haute couture costumes, but ready-to-wear propositions are not so familiar. Why is that? For many years technological limitations stopped designers from joining this technology on a broader scale. The most common, and cheapest 3D printers that operate in FDM technology ware limited to the quite stiff materials. Even flexible filaments weren’t cloth-like. That is why clothes made from it looked a little bit like armors. On the other hand, SLS technology capable of printing from more flexible materials was too expensive even to try. Everything changed in 2014 when SLS patent expired, and first desktop printers operating in this advanced technology appeared on the market. Thanks to devices like Sinterit Lisa it is now possible to print such detailed and small objects like flowers that can be attached to swimwear.

Fashion needs flexibility
– Most of our clients use hard materials like PA12. It becomes a standard for a broad range of industries. But fashion needs more flexible solutions – says Konrad Głowacki, one of the Sinterit Co-Founders. – It is not so easy to find a dependable, flexible material that would be a perfect match for the fashion industry and available for 3D printers. But as several years ago only a few people believed that SLS technology could become a desktop solution, available for every company, now we would like to go forward with the range of materials. After months of testing, we are happy to provide two reliable products: Flexa Black and Flexa Grey – adds Głowacki.
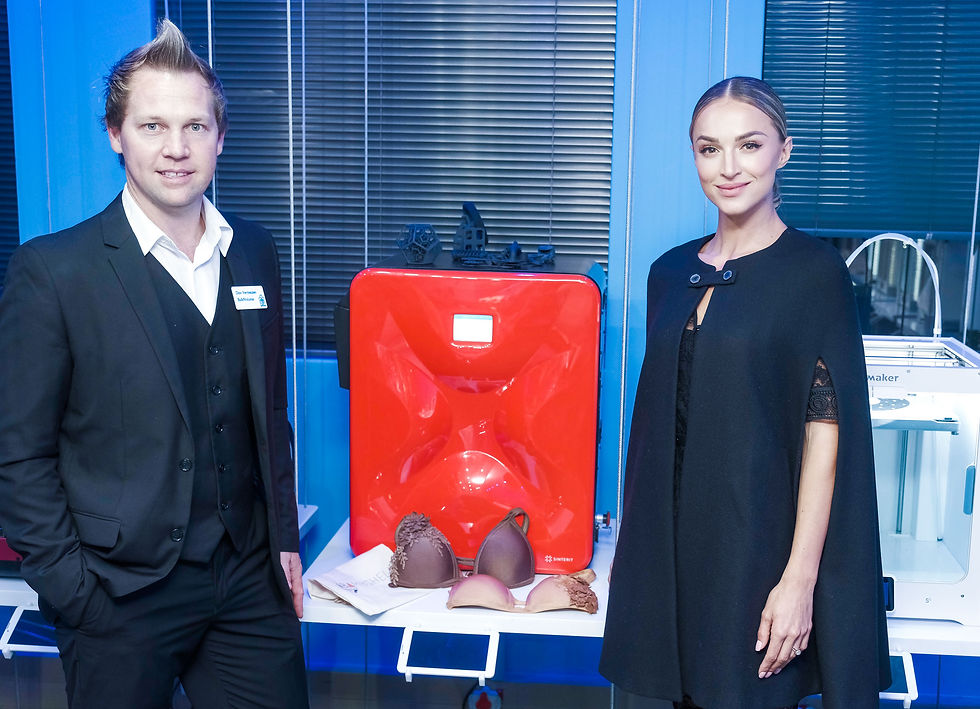
代发外链 提权重点击找我;
google留痕 google留痕;
Fortune Tiger Fortune Tiger;
Fortune Tiger Fortune Tiger;
Fortune Tiger Slots Fortune…
站群/ 站群;
万事达U卡办理 万事达U卡办理;
VISA银联U卡办理 VISA银联U卡办理;
U卡办理 U卡办理;
万事达U卡办理 万事达U卡办理;
VISA银联U卡办理 VISA银联U卡办理;
U卡办理 U卡办理;
온라인 슬롯 온라인 슬롯;
온라인카지노 온라인카지노;
바카라사이트 바카라사이트;
EPS Machine EPS Machine;
EPS Machine EPS Machine;
EPS Machine EPS Machine;
EPS Machine EPS Machine;
무료카지노 무료카지노;
무료카지노 무료카지노;
google 优化 seo技术+jingcheng-seo.com+秒收录;
Fortune Tiger Fortune Tiger;
Fortune Tiger Fortune Tiger;
Fortune Tiger Slots Fortune…
站群/ 站群
gamesimes gamesimes;
03topgame 03topgame
EPS Machine EPS Cutting…
EPS Machine EPS and…
EPP Machine EPP Shape…
Fortune Tiger Fortune Tiger;
EPS Machine EPS and…
betwin betwin;
777 777;
slots slots;
Fortune Tiger Fortune Tiger;
google 优化 seo技术+jingcheng-seo.com+秒收录;
谷歌seo优化 谷歌SEO优化+外链发布+权重提升;
Fortune Tiger Fortune Tiger;
Fortune Tiger Fortune Tiger;
Fortune Tiger Fortune Tiger;
Fortune Tiger Slots Fortune…
gamesimes gamesimes;
站群/ 站群
03topgame 03topgame
betwin betwin;
777 777;
slots slots;
Fortune Tiger Fortune Tiger;
谷歌seo推广 游戏出海seo,引流,快排,蜘蛛池租售;
Fortune Tiger…
Fortune Tiger…
Fortune Tiger…
Fortune Tiger…
Fortune Tiger…
gamesimes gamesimes;
站群/ 站群
03topgame 03topgame
google seo google seo技术飞机TG-cheng716051;
03topgame 03topgame
Jogos JOGOS
Fortune Tiger Fortune Tiger;
Fortune Tiger Slots Fortune Tiger…
Fortune Tiger Fortune Tiger;
EPS машины EPS машины;
Fortune Tiger Fortune Tiger;
EPS Machine EPS Cutting Machine;
EPS Machine EPS and EPP…
EPP Machine EPP Shape Moulding…
EPS Machine EPS and EPP…
EPTU Machine ETPU Moulding Machine
EPS Machine EPS Cutting Machine;